Outsourcing PCB Assembly, Test and Repair
- stevewoods9
- Aug 6, 2012
- 4 min read
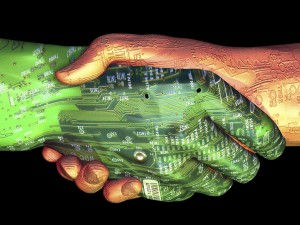
We were delighted to be asked to contribute an article for the September issue of Electronic Product Design (EPD) magazine, tackling the topic of outsourcing. If you do not subscribe to the magazine, please see the article below.
With the media intent on reporting on a global economy still struggling to kick on from the ravages of widespread recession and many of the World’s largest economies fully occupied balancing austerity measures against the demands for growth, it is easy to forget that many companies are having incredibly successful trading periods. Keen to exploit new opportunities, organisations are looking at how they can grow and expand their offering without having to expose themselves to unnecessary risk.
Outsourcing has been lauded as a solution for these companies, but is it the answer? In this article, Portsmouth-based electronic assembly, test and repair house, Soumac, explore what is involved in the outsourcing process, the pros and cons and what to look for if and when you decide to use an outsourced assembly, test and repair company.
Outsourcing – what is it and how is the sector performing?
Most organisations have a pre-conceived notion of what outsourcing is but to ensure we are all on the same page, our definition is:
“The act of one organisation contracting with a third-party provider to deliver services that might otherwise be performed in-house by employees.”
A recent study by KPMG into outsourcing, entitled ‘UK Service Provider Performance and Satisfaction (SPPS): 2012’, found that 76% of respondents stated they would continue to outsource and just under 20%, ‘certain to outsource more’.
It is clear that outsourcing is big business and affords a range of opportunities to companies keen to exploit the benefits. However, the study also identified that the industry must not take its clients for granted.
46% of respondents were unsure if they would recommend their service provider, 12% were dissatisfied and nearly 50% of those dissatisfied identified an inability of their service provider to recognise opportunities for innovation as a major factor. Nearly a third claimed agreements were not delivered on time or budget.
Outsourcing – The Pros and Cons
Clearly there are pros and cons to outsourcing, regardless of which sector you operate in. As electronic assembly, test and repair specialists, Soumac, have identified the following list of pros and cons to help you establish whether outsourcing is right for your organisation.
The Pros:
Cost savings – 70% of respondents in KPMG’s study identified this as a key driver for outsourcing. For small or medium batches it is generally more cost effective to outsource, avoiding the need for additional investment in equipment that may be used relatively infrequently or as a one-off.
Access to specialised staff – 61% of those surveyed claimed this was an important aspect of outsourcing. Having to recruit in experts is costly. Utilising outsourcing specialists gives you access to industry experts, without the hassle, cost and difficulties of recruitment.
Benefit from focused Quality Systems. All good electronic assembly companies should maintain Quality Systems, ensuring a consistent and reliable delivery of high quality products and services. As an example, Soumac hold ISO9001:2008 and ISO14001:2004 certifications.
Financial flexibility – companies that outsource value not only the savings it affords but also the financial flexibility that comes with it. Gone are the days of 10 year deals. Today, shorter term agreements with easy renewals dominate, giving companies security and financial flexibility.
A single point of contact – some electronic assembly companies provide a full turnkey service, including: procurement of materials, assembly, test and repair, giving clients a single point of contact to manage all their requirements.
Enhanced capacity management – companies that outsource are better placed to manage peaks and troughs in their order book, ensuring they do not have unnecessary and wasteful redundant capacity.
Speeding up time to market – companies like Soumac specialise in helping clients speed up the time to market of new products. By delivering low volume prototypes rapidly and identifying early on in the manufacturing process potential pitfalls, clients can avoid costly and time consuming problems during high volume production. Guaranteeing manufacturability and the checking of documentation to ensure it reflects what is needed should be key components of an electronic assembly service.
The Cons:
Documentation has to accurately reflect requirements – whilst one would expect this to be the case in any event, it is important to note that if it isn’t, problems occur and relationships can deteriorate quickly.
Once tooling has been procured by your chosen electronic assembly company, it is easy to feel tied to that outsourcer and reluctant to change.
We often hear from organisations new to outsourcing that they experience insecurity around a perceived loss of control. This can be easily overcome by clear and consistent communication between the two organisations.
When outsourcing to an organisation based abroad, where English is not the mother tongue, some companies have experienced difficulties arising from language barriers. This has resulted in miscommunication between the two parties and less-than-satisfactory service and quality levels. Utilising companies that employ fluent or native speakers helps mitigate this risk.
Conclusions
To outsource or not to outsource, that is the question. It is self-evident that outsourcing comes with risks attached; however, many of these risks exist whether you outsource or undertake the task inhouse.
The sheer size of the outsourcing industry illustrates that many companies feel the benefits of outsourcing more than overwhelm the risks and concerns.
The costing savings, scalability, access to industry experts, experience and sense checking afforded by a quality electronic assembly partner are all compelling reasons for companies new to outsourcing to give it a go.
To those already involved, make sure that your existing suppliers are delivering on what they promise and looking for every opportunity to innovate and add value. If they are not, consider reviewing your outsourcing partners.
Comentários